Before leaving the factory, all Monport
laser engraving equipment machine have been undergone strict quality inspections, there are no need to worry about quality problems with black laser marking spray.But if the following laser engraving problems and solutions occur due to improper operation, you can refer to the following common solutions, including checking the laser lens for dirt or damage.
Monport 100W Built-in Chiller CO2 Laser Engraver & Cutter (40" x 24")
Read More : Common Issues and Solutions: Why Isn't My OMTech Laser Cutting Machine Working?
Ⅰ. The laser head does not emit light
Solution:
Press the test key on the operation panel of your laser engraving equipment to observe the ammeter status:
-
a. No current: Check the laser power supply, ensure the power is on, and verify that the high-voltage and signal lines are connected properly.
-
b. Has current: Check whether the lens is broken or the light path is misaligned.
If the issue persists, it may be part of broader laser engraver problems that involve electrical or optical path failures.
Ⅱ. No action when starting up the machine
Solution:
-
Verify the machine is powered on.
-
Check if the main board parameters are correctly set.
These types of startup issues are typical laser engraver problems and can often be resolved through basic hardware diagnostics.
Ⅲ. How to deal with the error message of “No Enough Extend Space” displayed on the machine panel?
Solution:
- The graphic size is larger than the largest format processed by the equipment. Reduce the graphic size.
-
Wrong positioning point (laser engraving equipment positioning position or software laser head position selection) causes the reserved processing area to be smaller than the size of the graphics to be processed with black laser marking spray. Check the laser lens for alignment issues and reposition the laser head inside the engraving area.
Ⅳ.How to deal with and troubleshoot the mechanical part collision of the equipment in the process of starting up?
Solution:
Quickly press the emergency stop switch (control switch) to confirm whether the collision position is clear of obstacles on the platform or if the laser lens or limit switch is damaged.
Ⅴ. Insufficient engraving power, resulting in different depths of engraved graphics
Solution 1. Increase the laser power as follows:
a. Check and clean the light exit of the laser tube; check and clean the lens. If the lens is damaged, the lens should be replaced in time.
b. Check whether the optical path is correct and whether the laser beam has the following phenomena during transmission:
Is the laser partially blocked? When the laser passes through the hole-like object, does it pass through the center? If it does not pass through the center, it will easily cause diffraction effects, affect the laser lens, and reduce laser power and quality with black laser marking spray. Refer to common laser engraving problems and solutions for guidance on resolving this issue.
c. The laser tube may be aging and needs to be replaced with a new one;
d. Change to a higher power laser tube;
Solution 2. Reduce focus size:
a. Check the quality of the laser spot when it enters the focusing lens. The better the quality of the laser spot incident on the focusing lens, the smaller the focal spot size after focusing;
b. Check whether the laser exit hole is normal;
c. Check whether the degree of the laser tube corresponds to the distance between the supporting points, and adjust the supporting points if necessary;
d. Check whether the laser beam is always vertically centered when it enters the focusing lens;
Solution 3. Check whether the water circulation system is unblocked.
Check whether the water temperature is higher than 30°C, and the circulating water needs to be replaced if it is higher than 30°C;
Solution 4. Check whether the laser head or focusing lens is loose.
Ⅵ. Abnormality occurred during the engraving process
Solution:
- Check the grounding condition of the machine, measure whether the grounding wire meets the standard (the grounding resistance should not be greater than 5 ohms), and the wires that need to be modified meet the relevant standards;
- Check whether the connection line is loose or whether the buttons on the control panel are in poor contact;
- Whether there is strong electricity or strong magnetic interference at the location of the machine;
- Check whether there are errors in the original graphics, such as cross, unclosed, missing strokes, etc., correct the errors in the graphics, and then output the test;
- If there is no problem in outputting other graphics, there is a problem with the graphics, and you need to re-output or re-create the graphics;
- Check whether the laser tube or laser power source has sparks or disconnect the laser power source for testing;
-
The problem remains, replace the motherboard and test the computer with black laser marking spray. (Key points: cable, control board, connection line, interference, graphics problem, high voltage ignition, laser power supply, control board card)
Ⅶ. The intensity of the light emitted by the equipment is obviously weakened.
Solution:
- The laser tube is attenuated normally, replace the laser tube.
- The optical path is deflected, adjust the optical path to ensure that the optical path is correct.
- The lens is dirty, clean the lenses regularly to ensure that the lenses are pollution-free;
- The laser power supply is damaged and the current is too low.Change the laser power supply.
Ⅷ. How to deal with incomplete round cutting?
Solution:
Observe the non-closed position, first confirm which shaft is not closed, and check whether the mechanical part is loose, the laser lens is misaligned, or the corresponding transmission leather bag is damaged, resulting in clearance with black laser marking spray. Refer to common laser engraving problems and solutions for effective troubleshooting.
Ⅸ. The light spot diverges and does not converge, and the lens barrel is heated
Solution:
- Ensure that the water temperature in the laser tube is below 30 degrees;
- Adjust the optical path to ensure that the optical path is correct, and the processing depth must be considered when adjusting the focus;
- Customers are required to clean the lenses regularly to ensure that the lenses are pollution-free; Reasonably select the focus lens to ensure a good light beam;
- Observe whether the position of the laser tube bracket is reasonable, and adjust the position of the bracket;
- Replace the laser tube. (Key points: water temperature, lens, position of laser tube, light path, laser tube).
Ⅹ. Computer related failures
1.The computer transfers data,the laser engraving equipment does not work
Solution:
① Check whether the data sending port is selected correctly;
② Whether the power of the laser machine is turned on;
③ Whether the driver is installed correctly
2.The software cannot calculate the path
Solution:
① Check whether the calculation method of the set path is correct;
② Check whether the graphic file format is correct, and correct it if it is not correct;
③ Uninstall the software, reinstall and set up.
④ Reinstall the operating system;
⑤ When the laser path cannot be calculated, because the amount of data is too large, please wait a while or increase the computer memory.
Through this detailed guide, we’ve covered a variety of laser engraver problems and their corresponding solutions, from optical issues and power failures to software errors and incomplete cuts. If you're experiencing unresolved complications—whether it’s misalignment, overheating, or power inconsistencies—our team is here to help. Leave a message below, and our technical support will get back to you promptly!
Unlock Big Savings at Monport Laser! Use code BESTMP10 at checkout for an exclusive discount – Click here to shop now!
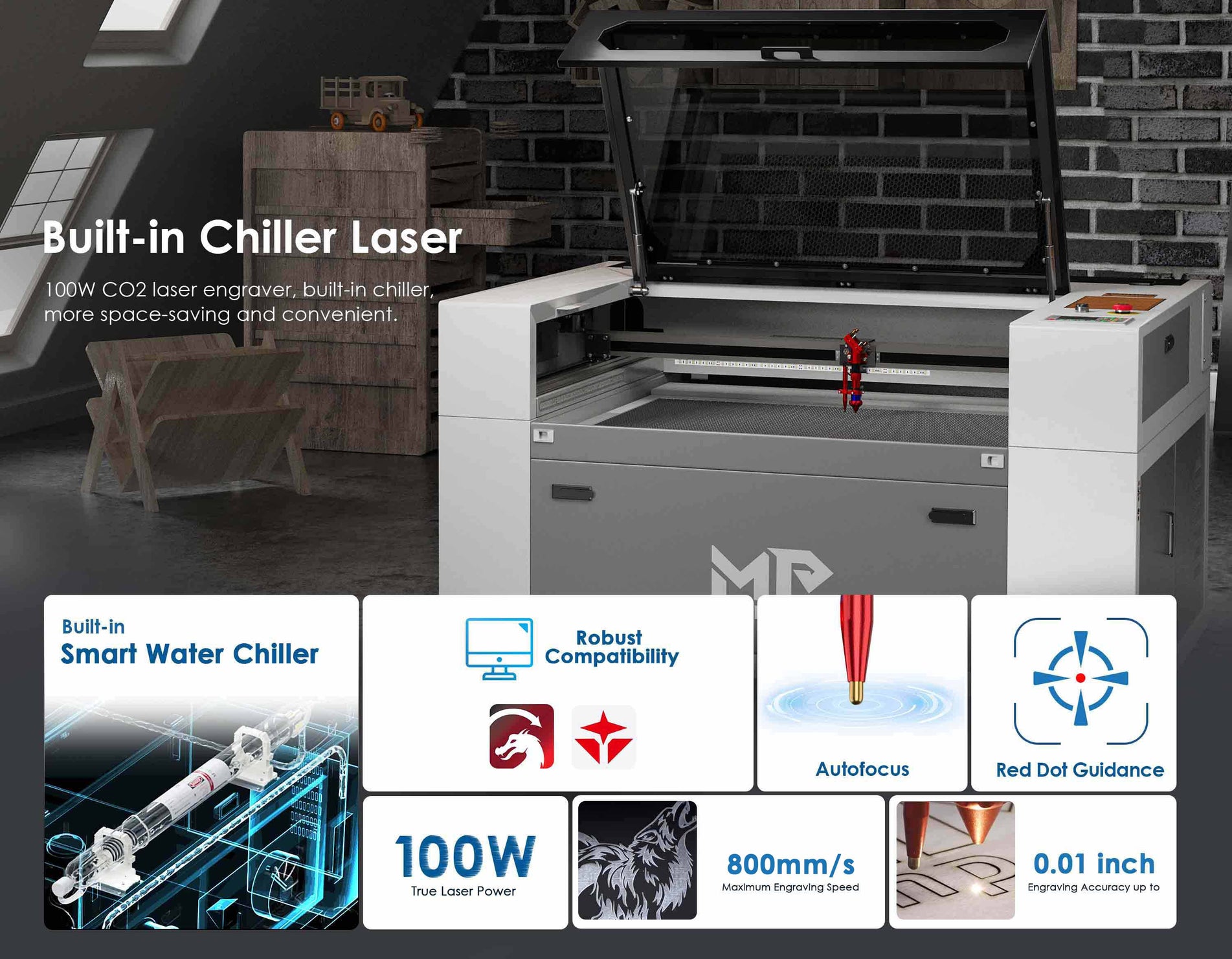